Implementing RFID retail inventory management offers numerous benefits, including improved accuracy, efficiency, and real-time tracking. As retailers seek to optimize their operations and enhance the customer experience, adopting best practices for RFID implementation becomes crucial. This guide explores the essential steps and strategies for successfully integrating RFID into retail inventory management systems.
Highlights
- RFID technology revolutionizes inventory management by offering real-time tracking and significantly improving accuracy and efficiency.
- There are two main types of RFID tags: passive (cost-effective for short ranges) and active (battery-powered for long ranges), and two types of readers: fixed (stationary) and handheld (portable).
- Integrating RFID with POS systems streamlines the checkout process, reduces wait times, and enhances inventory accuracy through automatic stock updates.
The Impact of RFID Retail in Inventory Management
RFID (Radio Frequency Identification) technology is transforming retail inventory management by streamlining tracking and counting processes. Traditional methods, like manual inventory counts, are often inaccurate and labor-intensive. RFID provides real-time inventory tracking, reducing errors and ensuring optimal stock levels. It’s like hitting two birds with one stone—saving money while enhancing customer satisfaction.
In the supply chain, RFID increases efficiency by automating data collection and facilitating product movement from suppliers to shelves. It handles receiving, picking, and packing, improving accuracy and speeding up shipping while minimizing delays and bottlenecks.
RFID retail inventory management improves the customer experience by keeping products consistently available and minimizing out-of-stock issues. It also speeds up the checkout process with RFID self-checkout stations, allowing customers to scan all their items at once, significantly reducing wait times.
Moreover, RFID personalizes shopping by gathering data on customer preferences and behaviors. This information helps retailers tailor products and offers to individual customers, improving overall efficiency and enriching the shopping experience.
5 Best Practices to Implement RFID in Retail Inventory Management
Select the Appropriate RFID Tags and Readers
Due to the world’s increasing digitization, the logistics industry has undergone several innovation processes, such as using RFID technology to track products being stored.
In 2020, the inventory tags market was valued at almost five billion U.S. dollars and is projected to reach over 7.2 billion U.S. dollars by 2028.
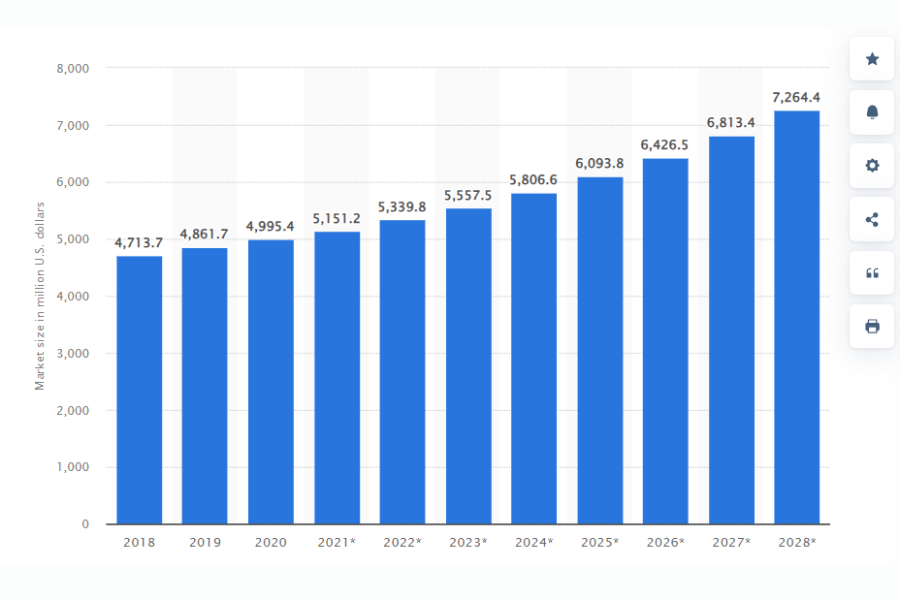
This growth is largely driven by the adoption of RFID retail inventory management. This technology includes two key components: RFID tags and RFID readers. RFID tags are tiny electronic devices that store and transmit data via radio waves, while RFID readers are devices designed to scan and retrieve this data.
When choosing RFID tags and readers for retail inventory management, consider the following factors to ensure optimal performance:
Type of RFID Tags:
- Passive Tags: These tags lack an internal power source and rely on the reader’s signal. They’re cost-effective and suitable for shorter ranges.
- Active Tags: Equipped with an internal battery, these tags support longer-range transmission. They’re ideal for applications needing more range and durability.
Type of RFID Readers:
- Fixed Readers: Installed in specific locations, they continuously scan and monitor inventory at entry and exit points.
- Handheld Readers: Portable devices for on-the-go scanning and real-time inventory checks. They’re useful for physical audits and managing stock in various locations.
Carefully evaluating these factors will help you choose the most suitable RFID tags and readers for your retail inventory management system. This will ensure enhanced accuracy, efficiency, and reliability in tracking and managing your inventory.
Test and Monitor Your RFID System
Before rolling out your RFID retail inventory management system,conduct extensive testing so that it will performs as expected and achieve your inventory management objectives.
Follow these steps for effective testing and monitoring:
- Thorough Testing: Test all components, including tags, readers, and software, to ensure they work seamlessly together and meet inventory management requirements. Assess read range, accuracy, and integration with existing Enterprise resource planning (ERP), warehouse management system (WMS), and POS systems.
- Regular Monitoring: Continuously check system performance for issues such as tag read failures, reader malfunctions, and software glitches. Implement real-time alerts to address problems promptly.
- Issue Detection and Resolution: Develop a proactive maintenance schedule to address potential issues. Quickly replace faulty components and troubleshoot problems by checking connections, recalibrating equipment, and adjusting settings.
- Performance Evaluation: Measure the return on investment (ROI) by comparing benefits like improved inventory accuracy and operational efficiency against system costs. Track key performance indicators (KPIs) such as read rates and processing times.
- Continuous Improvement: Collect user feedback and stay updated on technological advancements. Use insights to refine processes and consider upgrades to enhance system performance.
Integrate RFID with your existing systems and processes
RFID brings noteworthy benefits for inventory management but works best when integrated with your existing systems and processes.
Here’s how to secure a smooth and effective integration:
- Integration with Existing Systems: Integrate RFID with ERP, WMS, and POS systems to enhance efficiency and accuracy. RFID synchronizes inventory data with ERP, improves WMS with real-time tracking, and automates POS transactions for faster checkouts.
- Data Consistency and Accuracy: Ensure that RFID data is consistently updated across all integrated systems. This prevents discrepancies between different platforms, ensuring accurate inventory records.
- Staff Training: Provide comprehensive training for your staff on using RFID technology. Teach them how to operate RFID hardware, interact with integrated systems, and handle data effectively.
- Update Policies and Procedures: Review and revise your policies and procedures to incorporate RFID technology. Document and communicate new workflows and data management practices to all relevant personnel.
By effectively integrating RFID with your ERP, WMS, POS, and other systems, you can maintain data accuracy, streamline operations, and ensure a seamless transition to RFID-enhanced inventory management.
Manage and analyze data with RFID software
RFID retail inventory management relies on software to collect, store, and analyze data from RFID tags and readers. This software is pivotal in managing and optimizing your inventory by offering several functionalities:
- Data Collection and Storage: RFID software aggregates data from RFID tags, including inventory levels, item locations, movements, and status. This centralized data repository supports accurate and real-time inventory management.
- Inventory Management: The software helps you track inventory across various stages, ensuring that you can monitor stock levels, manage product locations, and oversee item movements efficiently.
- Data Analysis and Reporting: RFID software provides tools for generating detailed reports and insights. These analytical capabilities allow you to evaluate inventory performance, identify trends, and make data-driven decisions to enhance operational efficiency.
Stay updated on RFID trends and innovations
To fully benefit from RFID technology, stay updated on the latest advancements. Emerging features and innovations can significantly enhance your inventory processes:
- Emerging Technologies: Stay informed about advancements such as cloud-based RFID for flexible data management, smart RFID for advanced analytics, and RFID sensors for real-time monitoring. These technologies can offer new capabilities and efficiencies.
- POS Systems with RFID Support: Look for POS systems that natively support RFID, such as ConnectPOS. These systems streamline the checkout process, reduce wait times, and improve inventory accuracy by automatically updating stock levels with each transaction.
- Networking and Insights: Connect with RFID users and experts to gain valuable insights and learn from their experiences. Participate in industry forums and events to understand best practices and how others are using new RFID technologies.
These approaches guarantee your inventory management system remains effective and up-to-date, helping you achieve your inventory goals and improve operational efficiency.
ConnectPOS – Your Reliable Inventory Management System
ConnectPOS is a comprehensive and advanced point-of-sale software, tailored to meet the demands of modern retail environments. the system integrates seamlessly with RFID retail inventory management to provide a robust and reliable inventory management system, ensuring that your business operates smoothly and efficiently.
Key Features and Benefits:
- Real-Time Inventory Tracking: ConnectPOS leverages RFID technology to offer real-time tracking of your inventory. This means you can monitor the exact location and status of each item at any moment, ensuring greater visibility and control over your stock.
- Enhanced Accuracy and Efficiency: By automating data collection, ConnectPOS reduces human errors linked to manual inventory tracking. This improves accuracy in inventory records, helping maintain optimal stock levels and preventing overstocking or stockouts.
- Seamless Integration: ConnectPOS smoothly integrates with your existing systems. This ensures data consistency across all systems, streamlines workflows, and enhances operational efficiency.
- Advanced Analytics and Reporting: With ConnectPOS, you gain access to powerful analytics and reporting tools. These features generate detailed reports on inventory performance to help identify trends and make data-driven decisions to optimize your management processes.
- Security: Data security is a top priority with ConnectPOS. The system includes robust security measures to protect your sensitive inventory data from unauthorized access and breaches, ensuring compliance with data protection regulations.
FAQs: RFID Retail Inventory Management
- How does RFID work in retail inventory management?
RFID tags are attached to merchandise, and RFID readers are used to scan these tags. This allows for real-time tracking of inventory, improving accuracy and efficiency in managing stock levels.
- What are the benefits of using RFID retail inventory management?
- Accuracy: Reduces human error in inventory counts.
- Efficiency: Speeds up inventory tracking and replenishment processes.
- Real-time data: Provides up-to-date inventory information.
- Loss prevention: Helps in tracking and preventing theft.
- Customer experience: Enhances stock availability and customer satisfaction.
- How does RFID improve inventory accuracy?
RFID eliminates manual counting errors and provides precise data on inventory levels, ensuring that stock information is accurate and up-to-date.
Conclusion
Adopting RFID retail inventory management can transform how retailers track and manage their stock, leading to increased accuracy, efficiency, and customer satisfaction. By following best practices for implementation, retailers can overcome potential challenges and fully leverage RFID’s advantages, ensuring a streamlined and effective inventory management system.
To further enhance your retail operations, consider integrating ConnectPOS, a comprehensive POS system designed to optimize your inventory management and provide seamless customer experiences. Contact us to learn how we can elevate your business by visiting our website today.